ВЫБРОСИТЬ НЕЛЬЗЯ ПЕРЕРАБОТАТЬ
Вторичная переработка полимеров и возвращение их в производство — важный тренд общемировой зеленой повестки. Однако в России более 90 процентов пластиковых отходов до сих пор отправляется на мусорные полигоны, в то время как в Японии аналогичный показатель составляет менее 10 процентов. Столь высокий разрыв объясняется отсутствием необходимой инфраструктуры, но это тот случай, когда действовать нужно всем: государству, гражданам, бизнесу.Старт развитию этого направления в ТЕХНОНИКОЛЬ дал завод по переработке вторичных полимеров в Хабаровске, запущенный в 2020 году. Эстафету подхватило предприятие в Ленинградской области, которое способно ежегодно перерабатывать в гранулу до 6,5 тысячи тонн полистирольных отходов, что в натуральных величинах соответствует более чем 400 миллионам вспененных подложек для овощей и фруктов. А в феврале 2022 года в орбите ТЕХНОНИКОЛЬ появился завод АО «РБ групп» в Гусь-Хрустальном — один из крупнейших в стране производителей синтетических волокон из дробленого пластика.
Давая вторую жизнь пластиковому мусору, мы не только убираем отходы с улиц и снижаем нагрузку на полигоны, но также экономим энергетические и природные ресурсы. Так, если изделие уже выпущено и однократно использовано, то на повторное формирование из него гранулы требуется меньше 10 процентов от той энергии, что была затрачена на производство первичного материала.
Являясь одним из крупнейших игроков отрасли, мы понимаем, насколько важно развивать экологичный и социально ориентированный бизнес. Уже много лет мы придерживаемся принципов безотходного производства, став одним из первых производителей строительных материалов в России, кто внедрил на своих предприятиях рециклинг отходов и некондиции. А еще озаботились тем, что происходит с нашей продукцией после того, как она отслужит свой срок.
Наши цели до 2026 года:
- на 20 процентов снизить расходы по электроэнергии и уменьшить водопотребление;
- в пять раз увеличить переработку пластиков и полимеров;
- в 10 раз — рециклинг отслуживших свой срок материалов.
ДАЛЬШЕ — БОЛЬШЕ
В октябре 2023 года в производственный контур ТЕХНОНИКОЛЬ вошло еще одно предприятие по переработке вторичных полимеров — завод «Фантастик Пластик», открытый в декабре 2019 года в Нижнем Новгороде. Автоматизированный контроль качества продукции в процессе производства позволяет с высокой точностью определять параметры для последующего категорирования. На предприятии также построен не имеющий аналогов в России исследовательский центр вторичных полимеров, который позволяет проводить множество экспериментов.Благодаря этому приобретению Корпорация замкнула полный производственный цикл переработки пластика: пустая бутылка отправляется не на мусорный полигон, а на нижегородский завод, где ее перерабатывают в ПЭТ-флекс — сырье для производства синтетического волокна. В Гусь-Хрустальном из него сделают ПЭТ-волокно, которое затем отправится на рязанский завод в качестве основного сырья для геотекстиля — конечного продукта с высокой добавленной стоимостью.
Интеграция завода «Фантастик Пластик» уже стартовала и продлится год. Мы синхронизируем бизнес-процессы во всех направлениях, уделив особое внимание повышению производительности труда, высокий уровень которой — наша визитная карточка. Завод ждет расширение штата более чем на 30 процентов и увеличение мощностей в полтора раза. Также в планах строительство нового производственного цеха и площадки для хранения сырья и готовой продукции.
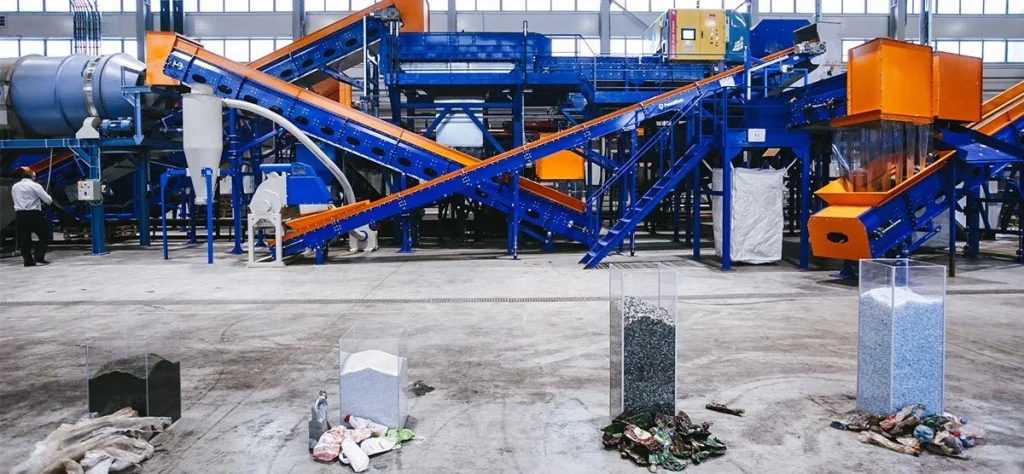
ПУТЬ БУТЫЛКИ
Ежегодно на нижегородской площадке будет производиться до 12 тысяч тонн ПЭТ-флекса из пластиковых бутылок. Для такого объема требуется 700 миллионов емкостей для напитков. Что именно происходит с ними на заводе, предлагаем узнать подробнее!Входной контроль. Пластиковые бутылки приходят на завод в виде прессованных кип. Это полигонное сырье, а потому достаточно загрязненное и требующее предварительной проверки на наличие в нем любого другого мусора, например пакетов, картона или металла. Всего при входном контроле оценивается более 10 параметров, включая цветовое соотношение: до 2022 года «Фантастик Пластик» перерабатывал два вида бутылок, прозрачные голубые и коричнево-зеленые, однако сейчас в дело идут только первые из-за отсутствия в их составе большого количества добавок и красителей. Если показатель засора превышает пять процентов, необходима дополнительная работа с поставщиком.
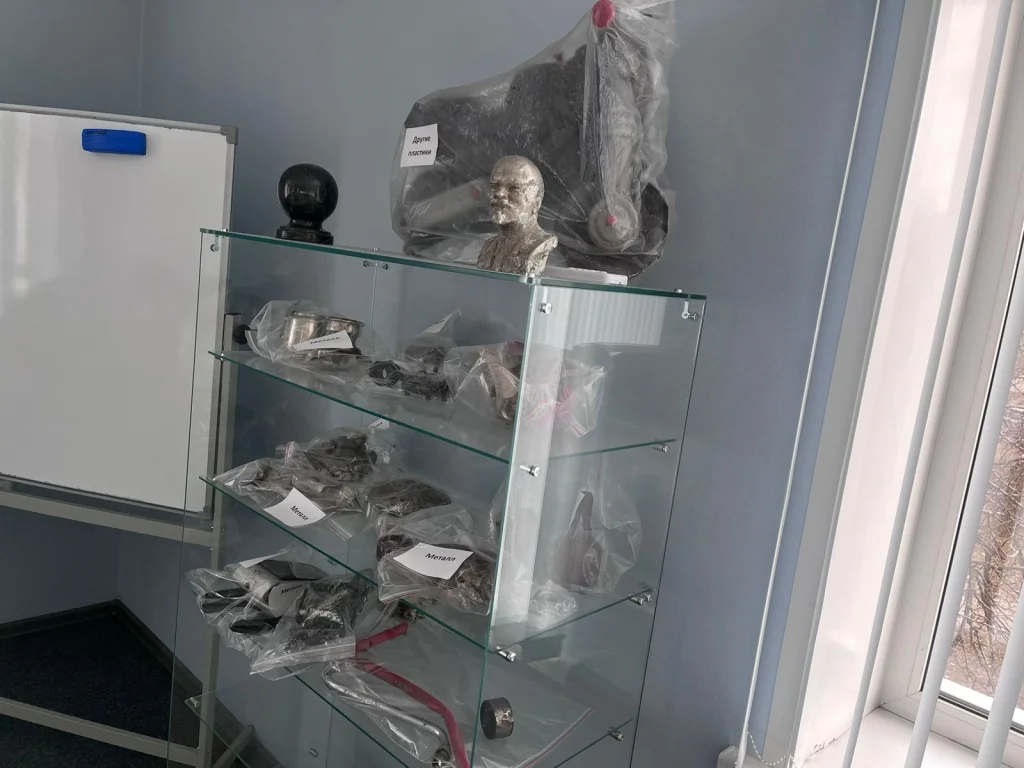
Мойка и сушка. Дробленый полуфабрикат первым делом поступает в сепаратор, где отделяются бумажные этикетки, затем — в ванну флотации. В ней происходит разделение пластиков по плотности: ПЭТ тонет, а крышечки с колечками всплывают. Последние, к слову, тоже идут в дело и передаются на линию ПНД на этом же предприятии, на которой ежегодно перерабатываются в гранулят порядка трех тысяч тонн соответствующего сырья.
Очищенный от этикеток и пробок полуфабрикат отправляется на горячую мойку со специализированными моющими средствами. Ранее для этого использовалась химия итальянского производства, но сейчас ведутся работы по импортозамещению и подбору альтернативных поставщиков, позволяющих не зависеть от геополитической турбулентности. Сама мойка производится в двух небольших чанах, которые работают параллельно. Цикл каждого составляет 250–300 секунд. Время и температура воды зависят от исходного сырья и технического задания на продукцию, которую требуется получить. Главное правило, как и со стиркой одежды: соблюсти баланс между эффективностью и сохранением физических свойств. При 90 градусах флекс, конечно, отмывается лучше, но меняет свою структуру, закручивается и приобретает желтый цвет.
Цикл мойки оканчивается двойным полосканием, окончательно убирающим все загрязнения и добавленные ПАВ и присадки, а также сушкой. Отработанная вода при этом отправляется в общую канализацию, но не сразу, а после прохождения нескольких систем очистки: от мелкой пыли, мусора, песка, грязи. Для этого на производстве установлено несколько специальных фильтров — решеток-песколовок.
Выходной контроль. После всех «спа-процедур» отмытый дробленый флекс вновь отправляется в оптический сепаратор, который доводит его фактически до премиального качества. На этом этапе важно еще раз пройти и металлоконтроль: даже самая маленькая алюминиевая банка способна забить целую партию продукции и нанести большой вред оборудованию.
Полученные хлопья засыпаются в биг-беги. Это мягкие контейнеры, в которых особенно удобно хранить и транспортировать сыпучие материалы. Из каждого биг-бега обязательно берется лабораторная проба, проверяющая насыпную плотность и размер частиц полученного ПЭТ-флекса, наличие остатков органики и других пластиков, а также другие важные параметры для оценки качества сырья продукции.
ДЕЛАЕМ МИР ЧИЩЕ ВМЕСТЕ
Вносить вклад в развитие зеленой повестки может и каждый из нас. Наши коллеги с нижегородской площадки подготовили небольшой список рекомендаций, которые позволят значительно упростить процесс переработки ПЭТ.- По возможности сдавайте пластиковые бутылки в специальные экопункты, которые стопроцентно отправят их по нужному адресу. Найти ближайшую к вам точку приема можно через Экологичный справочник России.
- Перед сдачей снимайте с бутылок этикетки и крышечки. Это позволит снизить отходность на производстве.
- Не кладите мусор в пластиковую бутылку. Особенно металлический. И особенно — в коричнево-зеленую бутылку. Увидеть этот мелкий мусор на производстве очень сложно, а его попадание в дробилку может быть губительно и для оборудования, и для качества получаемой продукции.