КРИЗИС КАК ВОЗМОЖНОСТЬ
Сокращение импорта в строительной индустрии началось еще в далеком 1998 году: из-за резкой девальвации рубля и роста внутреннего спроса его доля снизилась до 10 процентов. Этот период стал отправной точкой активного развития отечественной строительной промышленности, где ТЕХНОНИКОЛЬ сыграла ключевую роль.Последующие экономические качели — в 2008 и 2014 годах — сделали западные материалы еще более неконкурентоспособными для российского строительного рынка, что открыло большие возможности перед отечественными производителями. К примеру, когда мы запускали рязанский Завод монтажных пен в 2016 году, доля импорта составляла более 60 процентов. Для изменения этой ситуации на предприятии был создан собственный научный центр «Строительная химия», на базе которого разрабатываются новые и адаптируются под запросы потребителей существующие продукты. Как результат, ТЕХНОНИКОЛЬ получила признание рынка всего через три года, потеснив основных зарубежных конкурентов и войдя в топ-5 крупнейших производителей монтажных пен в России. С тех пор тренд на создание Корпорации строительных материалов и решений, которые зачастую опережают западных конкурентов, только усиливается.
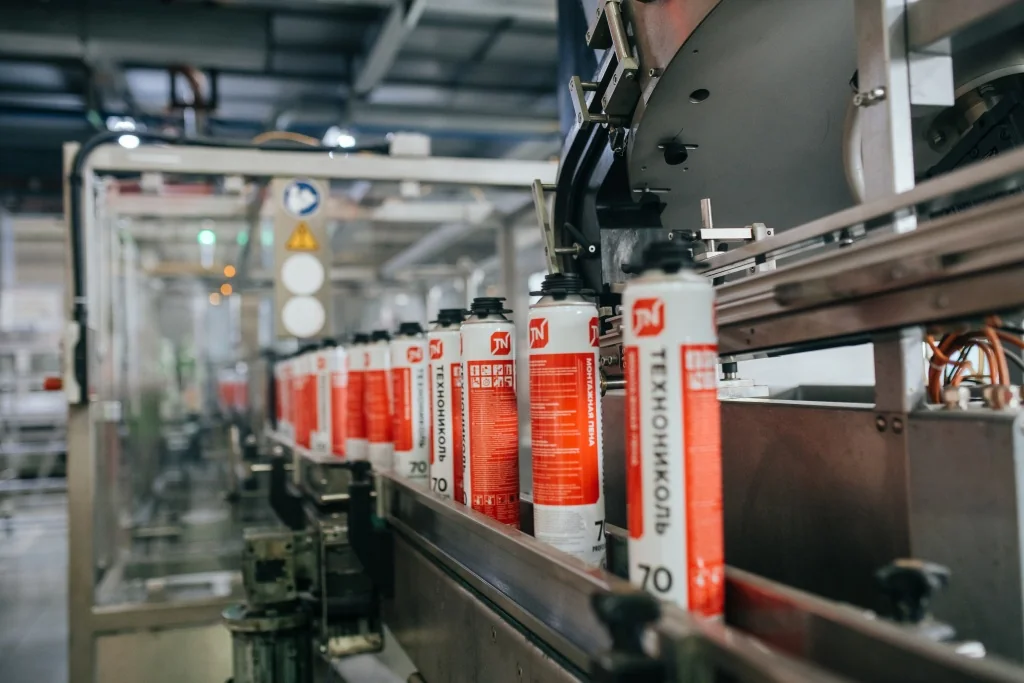
Еще один пример создания достойной альтернативы зарубежным поставщикам — производство судостроительной теплоизоляции, которое стартовало в 2016 году в Рязани на «Заводе ТЕХНО», затем — на предприятии в Хабаровске «ТехноНИКОЛЬ Дальний Восток». Потенциал нашей продукции связан прежде всего с соответствующим качеством, а также с удобной логистикой за счет размещения производства на территории России, что позволяет выполнять объекты госзаказа качественно и в срок. В наши дни судостроительную изоляцию выпускают уже на четырех заводах каменной ваты ТЕХНОНИКОЛЬ — в Белгороде, Рязани, Хабаровске и Челябинске, а ее поставки ведутся по всей стране, от Калининграда до Камчатки, на все виды судов и шельфовые проекты.
НОВЫЕ ВЫЗОВЫ
В 2022 году на арену вспорхнул очередной «черный лебедь», повлекший массовый уход зарубежных поставщиков. Дефицита на рынке самих материалов он не спровоцировал, поскольку последний почти полностью обеспечивается российской продукцией: по данным Министерства строительства и ЖКХ РФ, в 2023 году доля импорта строительных материалов и оборудования варьировалась от 5,7 процента для массового жилищного строительства до 22,8 процента для промышленных объектов. Однако риск дефицита, а в некоторых случаях и абсолютного прекращения производства материалов, все же возник. Все из-за того, что многие европейские виды сырья стали недоступны, на них выросли цены или изменилась логистика.В ТЕХНОНИКОЛЬ оказались готовы и к этому. «Еще в 2019 году, до всяких кризисов, имея пул альтернативных поставщиков по каждой группе сырья, мы решили, что у нас слабо проработана география. И в том же году мощно отработали Китай, — делится Екатерина Горячева, операционный директор СБЕ МиСХ. — К началу 2022 года у нас были китайские альтернативы по 90 процентам видов сырья. Что-то пришлось придумывать, где-то менять рецептуры, но фатальных провалов не было».
Корпоративную приверженность подходу «не класть все яйца в одну корзину» подтверждает Михаил Ольчев, директор рязанского завода «Лоджикруф»: «У нас в работе всегда есть сразу несколько поставщиков на случай, если какой-нибудь партнер по каким-либо причинам приостановит работу с нами. Например, у нас есть дублирующие поставщики в Азии. Поэтому у нас ни разу не было остановки производства из-за отсутствия сырья или компонентов, несмотря на все последние геополитические изменения».
Помог и опыт, накопленный в наших научно-исследовательских центрах (НИЦ), где специалисты постоянно проводят поиск наилучших решений, различные испытания, проверку качества продукции, а также создают собственные рецептуры, чтобы меньше зависеть от изменений на сырьевых рынках и всегда предоставлять качественные и доступные строительные материалы. «Сотрудники НИЦ и всех других подразделений нашей СБЕ, — рассказал Юрий Игошин, руководитель научного центра СБЕ БМиГ, — провели большую работу по поиску альтернативных видов сырья, например основ, полимерных модификаторов, защитных пленок и т. д. В лабораториях и на заводах были оперативно выполнены десятки экспериментов».
Юрий также отмечает важность синергии при решении подобных задач: «Отдел закупок разработал новые логистические маршруты для поставок сырья из Азиатского региона. Это позволило быстро заменить основные импортные сырьевые компоненты. Технический отдел БМиГ проделал кропотливую работу по поиску отечественных производителей оборудования для технологических линий. При этом качество продукции осталось на самом высоком уровне, а себестоимость не увеличилась значительно или осталась на прежнем уровне. Все это говорит о том, что только благодаря слаженной работе всех сотрудников из разных отделов и подразделений возможно оперативно и эффективно найти новые решения на вызовы кризисов».
Поиск аналогов дополняет второй путь: производить все, что нужно, самим. К примеру, раньше большую часть армирующей сетки для производства ПВХ-мембран мы закупали у европейских поставщиков, но после событий 2022 года этот материал попал в перечень товаров двойного назначения и стал недоступен для экспорта. Теперь же она производится на заводе «Лоджикруф» в Рязани, что позволило выйти на полный цикл производства ПВХ-мембран и закрыть на начальном этапе до 80 процентов собственных потребностей в армирующей основе. Аналогичная ситуация с тем же полиэфирным геотекстилем, предназначенным для дорожного и жилищного строительства. Запустив линию по его производству в Рязани в апреле 2024 года, мы также замкнули полный производственный цикл по ПЭТ — от сырья до готовой продукции высокого передела.
ПОДНИМАЕМ ОТЕЧЕСТВЕННОЕ МАШИНОСТРОЕНИЕ
Технологическое замещение остается для Корпорации одной из самых актуальных задач. До 2022 года основной фокус был направлен на приобретение комплектных технологий — от бункеров с сырьем до упаковочных машин. Сейчас цепочки прерваны, и ориентация на Азию не дает возможности приобрести комплектную технологию. Предприятия покупают отдельные узлы и своими силами стыкуют их. Так, ТЕХНОНИКОЛЬ развивает работу собственного конструкторского бюро, которое работает в тесном взаимодействии с инженерами из смежных отраслей. Ассортимент производимых им деталей огромен и достигает 1500 наименований ежегодно, включая штучные материалы.«Самая большая гордость — это когда получается выпустить оборудование по качеству и надежности лучше, чем на Западе. Ведь у нас принято считать, что технологии живут в Европе, а российское машиностроение находится в упадке. Мы своим примером доказываем обратное», — отмечает Игорь Глухов, руководитель учалинского предприятия «Кровмонтаж». Напомним, что на большинстве производственных площадок ТЕХНОНИКОЛЬ в той или иной мере установлено оборудование, изготовленное именно этим заводом. Подробнее рассказывали в 21-м номере «Технологий мастерства».
При должной поддержке такой работы можно рассчитывать, что в течение двух — трех лет появится реальная возможность заместить оборудование и производить его в России. Да, создать закрытые цепочки по оборудованию, металлу, станкам и упаковке — это вызов, но у нас есть все, чтобы ответить на него достойно.